
Are You Ready for
DRY ICE BLASTING?
Dry ice technology uses solid carbon dioxide (CO2) pellets as a blasting media. It is a non-abrasive and environmentally friendly method used to remove contaminants, coatings, and debris from various surfaces. Dry ice blasting is widely used in industrial and commercial applications with a focus on automotive, marine, and historical preservation.
Using compressed air, dry ice pellets are blasted onto the surface to be cleaned. The pellets rapidly convert from a solid to gas state in a process called sublimation. This natural reaction creates a micro-explosion on the surface, dislodging contaminants, coatings, and dirt without causing damage to the underlying material. The resulting gas dissipates into the atmosphere, leaving behind only the original intended surface.
KEY BENEFITS
-
Non-abrasive: Unlike traditional media blasting methods that use sand or other abrasive materials, dry ice blasting doesn't wear down or damage the surface being cleaned. This makes it suitable for delicate or sensitive surfaces.
-
No secondary waste: Since dry ice pellets sublimate into gas, there's no leftover blasting media to clean up after the process.
-
Environmentally friendly: Dry ice is made from recycled carbon dioxide, a naturally occurring gas. The process doesn't produce any hazardous waste or chemicals, making it a clear choice for those who care about the environment.
-
No water or solvents: Dry ice blasting is a dry process that is performed without the use of water or solvents, which will eliminate the potential damage inherent when seeking such high level cleaning results.
-
Versatile: Dry ice blasting can be used to clean a wide range of surfaces, from machinery and industrial equipment to sensitive electronics and historical artifacts. The gentle yet powerful process is capable of removing paint, grease, oil, adhesives, mold, soot, aged road debris, and other contaminants from surfaces. It's often used in industries such as manufacturing, automotive, food processing, aerospace, power generation and more.
BEFORE
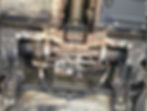
AFTER
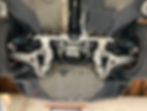